

This parameter is often not easily available and it is usually substituted for by a parameter such as the section thickness or upper surface ordinate just behind the leading edge. The boundary between the two depends on the leading edge radius, and the maximum lift for the first type varies with the same parameter. There are basically two types of stall, those in which the separation starts predominantly from just behind the leading edge and those which start from the trailing edge. The maximum lift coefficient in two-dimensional flow depends on the aerofoil section geometry, the surface condition (rough or smooth) and the Reynolds and Mach numbers. Russell MSc, MRAeS, CEng, in Performance and Stability of Aircraft, 1996 1.3.3 Maximum lift and the characteristics of flaps 5.3.1 Determination of the wing lift curve slope The rapid turnaround they provide is of great value in preliminary design situations in industry. However, it is important to develop some familiarity with empirical and approximate techniques rarely covered in academic courses. Such scientifically richer methods will generally have been covered in the fluid dynamics analysis courses of an engineering degree program and may be implemented, if desired. There are other, more sophisticated, approaches based on different computational fluid dynamics (CFD) schemes which will be discussed in varying degrees of detail. The methods that will be used to estimate C L, max for the various configurations of a wing are taken mainly from the USAF Stability and Control DATCOM, Hoak et al. Leading edge flap design and deflection angle. Trailing edge flap design and deflection angle. Wing aspect ratio A, taper ratio λ, and sweepback angle Λ. a.Īirfoil maximum lift coefficient c l, max. Only the most important of these will be considered here and they are listed below. You may also use a 2s pack that has a weight of 40grams to achieve the right balance.The maximum lift coefficient of the airplane C L, max depends upon many factors. This spififict setup uses the 450mah 3s pack with a weight of 40grams. If using the motor listed above, proper propeller will be 4×4.5L You may use plastic quad copter propellers also as long as its 4×4.5īattery we will use a 450mAh 3S LiPo Battery Pack 11.1V you are welcome to use a 2s instead but this will throw off the CG ( center of gravity) unless you move the battery back. With a weight of only 10 grams, it will produce ridiculous speeds with this MicroSonic wing.ĮMAX rs1306 version 2 brushless racing motor Motor used for this setup is the EMAX 1306 RS1306 4000KV version 5 gram servos can also be used, but taking note the more wight you add, the heavier the wing will get and torque will be lost. enough to hold your yank and banks with this fast micro wing. They are only 2.5 grams of and of torque. The Turnigy TGY-0025 Nano Servos work great with this setup. I like using XPS foam as its dense and light weight and virtually unbreakable. FoamĪny type of foam can be used for this micro wing project. You may use thick wire if you do not have carbon fiber, but again we want to keep this wing as light as possible for maximum speed, agility and ease of flight. Pushrods are also 1.5mm carbon fiber rods. You are welcome to use flat carbon fiber spar, just make sure its light weight, 4mm or 5mm might be too heavy. This will provide structural strength to the wings.
Flying wing airfoil pdf#
You may also use an old credit card or license, its plastic and very strong.Ĭlick here to download or print the PDF Version of the motor mount Wing Spar & Pushrodsįor the main wing spar, we use 3mm x 2mm hollow carbon fiber tube.
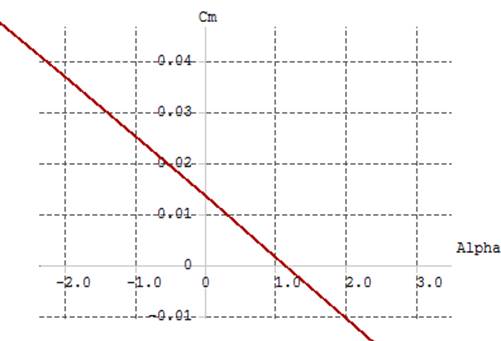
Trace outline and drill holes on a thin aluminum sheet or 2mm bass wood, plywood or any hard wood. If using the emax rs1306 motor mount motor, use this motor mount to print. In the build video i use 2mm hard balsa wood, its easy to cut with exacto knife and fairly rigid for hot wiring. Airfoils can be laser cut if you have access to a laser machine, or simply use balsa wood, or aluminum or even cardboard to cut out the shape of the foils.
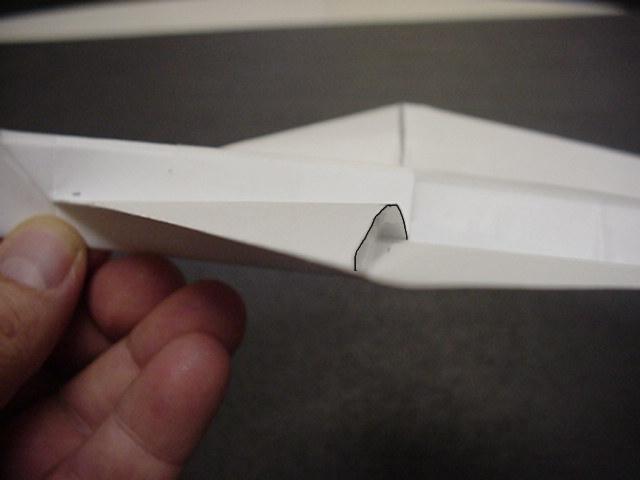
Right click on image and download to your computer. To download JPG lower resolution version of the plans below, right click on images below and save file.īelow are the airfoils we will use for root chord and tip chord. To print PDF version of the airfoils click here To print PDF version of one wing panel click here
Flying wing airfoil full#
To print PDF version of the full blue print Click here
